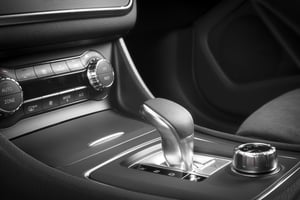
Fogging
Determination of the fogging behavior of materials used in vehicle interiors
FOGGING TEST IN THE
AUTOMOBILE INTERIOR
VISUAL ASSESSMENT OF THE PAINT QUALITY
A vehicle's paintwork is not only a design element, but also a key criterion for its perceived value and quality. At the same time, it protects the vehicle from external influences such as corrosion or mechanical damage. The inspection of paint surfaces is therefore a central component of quality control in order to detect and assess possible defects at an early stage. Our inspection methods enable precise analysis to make even the smallest defects such as bubbles, scratches, cracks or color deviations visible. These inspections provide detailed insights into the quality of the paintwork and its compliance with automotive industry specifications.
Experienced specialists examine the surfaces under different lighting conditions and with specialized tools such as light booths or magnifying glasses. We use standardized procedures to ensure that our assessments are objective and comprehensible. The results help to comprehensively assess the surface quality and identify potential areas for improvement. The visual inspection is carried out under controlled lighting conditions and from different viewing angles in order to detect defects comprehensively. Depending on the requirements, these inspections can be carried out manually or using optical measuring systems. Our procedures are based on the specifications of the automotive industry and international standards in order to provide reliable information about the condition of the paintwork.
The inspection methods are used in various areas of application. These include body parts such as hoods and doors, which are checked for large-area irregularities, as well as smaller, painted components such as bumpers or trim strips. Interior parts such as instrument panels or door panels are also inspected for gloss deviations and defects. For meaningful results, it is important that the samples are delivered in a clean and undamaged condition. Shockproof packaging prevents transport damage, while detailed information on the paint type, coating system and coating process makes it easier to adjust the test parameters.
The inspection includes the evaluation of the size and number of paint defects as well as possible deviations in gloss level or color that meet customer specifications. Standardized light sources such as daylight simulations and viewing from different angles enable precise analysis. Depending on the material and paint type, gloss measurements or reflection tests can also be carried out. As a rule, at least three painted samples or vehicle components are required for a test series, depending on the size of the components. Additional samples for repeat or comparative tests are recommended. The samples are shipped in shockproof packaging, accompanied by detailed information on the paint composition and coating thickness.
Our tests assess the quality of coatings to the highest standards and provide you with valuable insights into their condition. Contact us to find out more about our testing services!
Visual inspection methods
Fogging test methods
- DIN 75201-A (reflectrometric)
- DIN 75201-B (gravimetric)
- PV 3015 (Volkswagen)
- GMW 3235-A (General Motors Worldwide)
- PSA D45 1727
- and much more.
Are you looking for an exam? Standard? Specifications?
Accredited & certified tests
CONTACT OUR EXPERTS
Description. Lorem ipsum dolor sit amet, consetetur sadipscing elitr, sed diam nonumy eirmod tempor invidunt ut labore et
- Tab Title
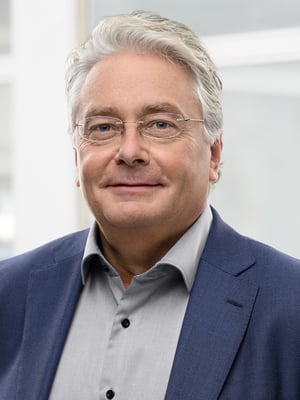
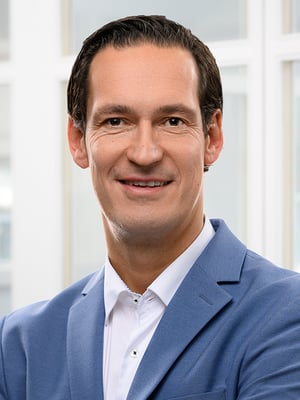
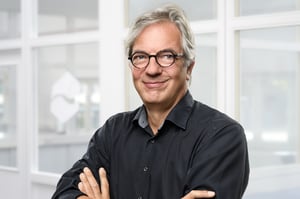
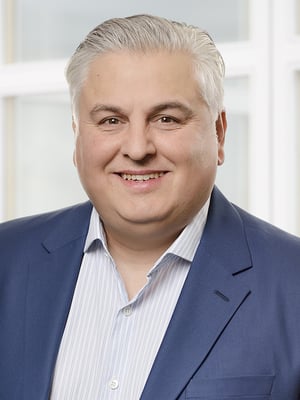
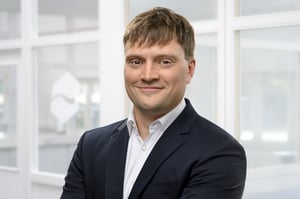
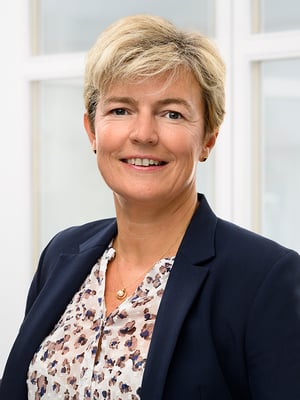
- 01 Purpose of the visual assessment
- 02 Test execution
Purpose of the visual assessment of paint surfaces
- Quality assurance: Identification of defects such as bubbles, scratches, cracks or color deviations to assess the paint quality.
- Compliance with standards: Verifying that paint finishes meet automotive industry specifications and customer requirements.
- Aesthetic evaluation: Ensuring a flawless appearance for a high-quality overall impression.
- Functional analysis: Checking whether the paintwork fulfills its protective function against external influences such as corrosion and mechanical damage.
- Optimization potential: Identifying weak points in order to make improvements to the paintwork or the production process.
Test execution
Visual inspection is usually carried out under controlled conditions using a light source and various viewing angles to make potential defects visible. Standardized procedures and tools such as light booths and magnifying glasses are used. Inspections can be carried out manually by specialists or using optical measuring systems, depending on customer requirements.
The process is based on automotive industry specifications and international standards to ensure an objective assessment of surface quality.
Frequently asked questions about the fogging test
The sample quantities required for a fogging test depend on the standard and the test method used. Here are the general guidelines:
1. standard DIN 75201 (type A and type B)
-
Type A (glass plate method):
A sample quantity of 10 cm² is typically required. The sample is placed on a heated plate in a sealed chamber and the volatiles released condense on a glass plate above. -
Type B (aluminum foil method):
Similar to type A, a sample volume of approximately 10 cm² is used. However, the volatile substances condense on a cooled aluminum foil.
2. standard ISO 6452 (international standard)
- Sample quantity:
Again, a sample size of about 10 cm² is typically required to evaluate the amount of volatiles released at elevated temperature.
3. other specific requirements
Depending on the specific requirements of the customer or OEM standards, sample quantities may vary. It is important to check the respective standards or test requirements carefully.
Method A - Reflectometric method:
- Principle: This method measures the change in reflectivity on a glass plate on which volatile components from the material sample are deposited.
- Procedure: A material sample is heated in a beaker while a glass plate above it is cooled to 21°C. The temperature difference causes the volatile components to condense on the glass plate. The reflectance index of the fogged glass plate is then measured to determine the amount of condensed material.
- Application: This method is particularly suitable for materials for which an exact determination of the optical fog effect is required.
Method B - Gravimetric method:
- Principle: This method measures the weight of condensed volatiles on an aluminum foil.
- Procedure: The material sample is heated in a beaker while an aluminum foil disc is cooled to 21°C. After 16 hours, the amount of condensed material on the foil is weighed.
- Application: This method is ideal for an accurate quantitative determination of the amount of condensed volatiles.
CONTACT US
CORROSION
Formaldehyd in Fahrzeugen: Herausforderungen für die Automobilindustrie
Read moreStellantis: Freigabe für Emissionsprüfungen erfolgreich (VIAQ)
Read moreVDA 277 vs. VDA 278: Was ist der Unterschied?
Read moreGeruchsunterschiede bei Polypropylen: Die Rolle von Faserverstärkung und Verarbeitungsparametern
Read moreWarum sind die Einheiten der Ergebnisse von Prüfungen der Werkstoffemissionen eigentlich so unterschiedlich?
Read moreGrenzwerte für Formaldehyd und Formaldehydabspaltern in Fahrzeugen
Read moreFREQUENTLY ASKED QUESTIONS ABOUT VISUAL INSPECTION
The samples should be delivered clean, free from damage and contamination. Shockproof packaging protects them from damage during transportation. Information on the type of coating, coating system and coating process is necessary in order to optimally determine the test parameters.