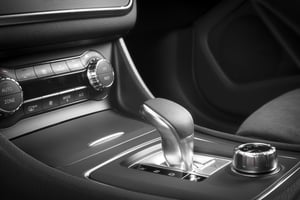
Fogging
Determination of the fogging behavior of materials used in vehicle interiors
FOGGING TEST IN THE
AUTOMOBILE INTERIOR
TESTS ON THE CHEMICAL RESISTANCE OF PAINTS
A vehicle's paintwork is more than just a visual accent - it plays a key role in protecting the vehicle from environmental influences and contributes significantly to its durability and lasting value. In the automotive industry in particular, vehicle paintwork is exposed to extreme conditions. They not only have to withstand impacts, scratches and the effects of the weather, but also a wide range of chemicals that occur during daily operation. These include aggressive substances such as road salt, petrol, diesel, brake fluids, oils and cleaning agents, which can attack the paint surface and significantly impair its protective function.
The chemical resistance of paintwork is therefore a decisive quality factor to ensure that the paintwork fulfills its protective function in the long term. A vehicle whose paint is not sufficiently resistant can suffer corrosion damage more quickly, which impairs both safety and appearance. Especially at high speeds or in challenging environments, such as in coastal or winter regions with high levels of road salt, the demands on the chemical resistance of the paintwork are particularly high.
It is therefore essential for car manufacturers and suppliers to test the chemical resistance of their paintwork using stringent test procedures. These tests ensure that the paintwork remains stable even under extreme chemical stress and does not show any damage such as discoloration, cracking, blistering or peeling. Comprehensive and precise tests are the only way to identify weak points at an early stage and improve paint quality in the long term.
Tests for resistance to chemicals:
Our chemical resistance tests simulate realistic scenarios in which vehicle paintwork comes into direct contact with aggressive substances. The aim is to analyze the effects of these chemicals on the paint layer and ensure that the coating retains its protective function even under extreme conditions. These tests are an essential part of guaranteeing the longevity and quality of your vehicle paintwork.
Efficient test methods for chemical resistance:
Tests for resistance to chemicals are carried out in accordance with industry-specific standards and guidelines. This involves exposing painted samples to defined chemicals such as acids, alkalis, solvents or fuels under controlled conditions. Different scenarios - from long-term exposure to short-term strong effects - are simulated according to customer requirements. The paintwork is then examined for possible changes, including color deviations, loss of gloss or structural damage.
The areas of application for these tests are diverse: body components are tested for their resistance to fuels and road salt, while plastic and metal parts for the vehicle interior are tested for their resistance to cleaning agents and chemicals. Engine compartment components, on the other hand, are tested for their resistance to oils, coolants and brake fluids.
In order for the tests to be carried out properly, the samples must be delivered in perfect condition without damage or contamination. Shockproof packaging is necessary to avoid damage during transportation. In addition, information on the coating composition and the coating systems should be enclosed.
The limit values for chemical resistance define clear requirements: Maximum tolerances for gloss or color changes, no peeling or blistering and the preservation of the corrosion protection function after exposure. The tests are carried out in accordance with ISO standards or manufacturer specifications and include tests with typical automotive chemicals such as petrol, diesel, brake fluid, road salt and cleaning agents. The duration and concentration of chemical contact and temperature conditions are customized to accurately simulate real-life exposure scenarios.
For reliable results, we recommend additional samples for possible repeat or comparative testing. The samples should be sent to our test laboratory in shockproof packaging, including information on the coating composition, the coating systems and the drying method.
Please contact our experienced team for more information.
Stone impact test methods
- DIN EN ISO 11643
- BMW AA-0055, test method 1/2/3..
- BMW AA-P 194, test method 1/2
- and much more.
Fogging test methods
- DIN 75201-A (reflectrometric)
- DIN 75201-B (gravimetric)
- PV 3015 (Volkswagen)
- GMW 3235-A (General Motors Worldwide)
- PSA D45 1727
- and much more.
Are you looking for an exam? Standard? Specifications?
Accredited & certified tests
CONTACT OUR EXPERTS
Description. Lorem ipsum dolor sit amet, consetetur sadipscing elitr, sed diam nonumy eirmod tempor invidunt ut labore et
- Tab Title
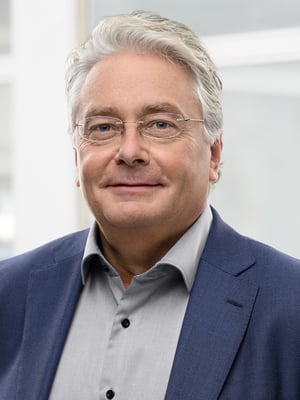
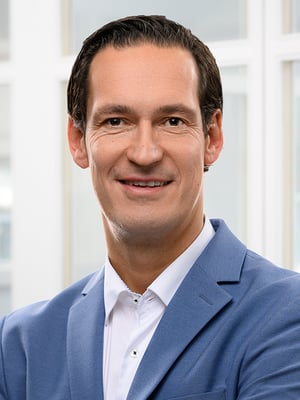
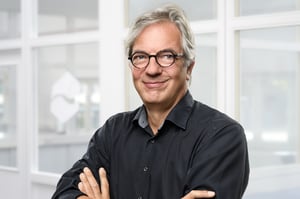
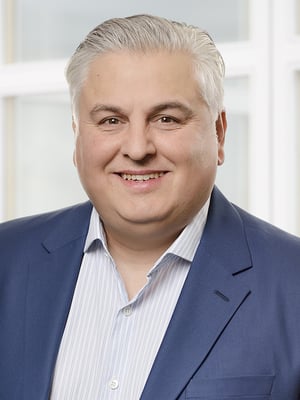
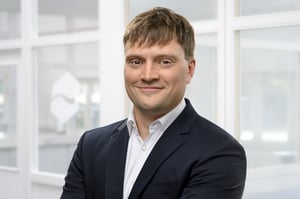
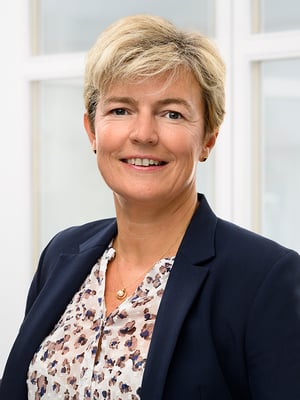
- 01 Purpose of chemical tests
- 02 Test execution
Purpose of chemical tests
- Determination of the chemical resistance of materials to various substances.
- Proof of the quality and durability of paintwork and surfaces.
- Ensuring the functionality of components under chemical stress.
- Prevention of damage such as color change, loss of gloss or peeling.
- Maintaining the corrosion protection function after contact with chemicals.
- Simulation of real stress scenarios in vehicle operation.
- Compliance with standards and manufacturer specifications for product safety.
- Identification of weak points in the material or coating system.
- Ensuring suitability for the area of application, e.g. interior, engine compartment or bodywork.
Test execution
The stone impact tests are carried out in accordance with the DIN EN ISO 20567-1 standard in order to simulate realistic stresses caused by stones and road dirt being thrown up. Standardized chilled cast iron granulate is shot at the samples to be tested at a defined pressure and angle. The test system makes it possible to vary the pressure and therefore the speed of the granulate, as the firing speed cannot be set directly in km/h. This ensures precise adjustment of the test parameters. This ensures precise adjustment of the test parameters to real load situations.
In order to achieve reproducible results, the test system is regularly calibrated and the granulate is routinely replaced. Depending on standard or manufacturer specifications, parameters such as grain size, bombardment quantity, angle and pressure can be flexibly adjusted.
Once the tests have been completed, the extent of the damage is visually assessed. The affected layers are documented and the results analyzed in accordance with the normative specifications. To ensure reliable performance, it is important that the samples are delivered in a clean and undamaged condition. They are transported in shockproof packaging, accompanied by accompanying documents with details of the coating and layer information. This ensures that all relevant details are included in the test parameters and that a precise analysis is possible.
Frequently asked questions about the fogging test
The sample quantities required for a fogging test depend on the standard and the test method used. Here are the general guidelines:
1. standard DIN 75201 (type A and type B)
-
Type A (glass plate method):
A sample quantity of 10 cm² is typically required. The sample is placed on a heated plate in a sealed chamber and the volatiles released condense on a glass plate above. -
Type B (aluminum foil method):
Similar to type A, a sample volume of approximately 10 cm² is used. However, the volatile substances condense on a cooled aluminum foil.
2. standard ISO 6452 (international standard)
- Sample quantity:
Again, a sample size of about 10 cm² is typically required to evaluate the amount of volatiles released at elevated temperature.
3. other specific requirements
Depending on the specific requirements of the customer or OEM standards, sample quantities may vary. It is important to check the respective standards or test requirements carefully.
Method A - Reflectometric method:
- Principle: This method measures the change in reflectivity on a glass plate on which volatile components from the material sample are deposited.
- Procedure: A material sample is heated in a beaker while a glass plate above it is cooled to 21°C. The temperature difference causes the volatile components to condense on the glass plate. The reflectance index of the fogged glass plate is then measured to determine the amount of condensed material.
- Application: This method is particularly suitable for materials for which an exact determination of the optical fog effect is required.
Method B - Gravimetric method:
- Principle: This method measures the weight of condensed volatiles on an aluminum foil.
- Procedure: The material sample is heated in a beaker while an aluminum foil disc is cooled to 21°C. After 16 hours, the amount of condensed material on the foil is weighed.
- Application: This method is ideal for an accurate quantitative determination of the amount of condensed volatiles.
CONTACT US
CORROSION
Formaldehyd in Fahrzeugen: Herausforderungen für die Automobilindustrie
Read moreStellantis: Freigabe für Emissionsprüfungen erfolgreich (VIAQ)
Read moreVDA 277 vs. VDA 278: Was ist der Unterschied?
Read moreGeruchsunterschiede bei Polypropylen: Die Rolle von Faserverstärkung und Verarbeitungsparametern
Read moreWarum sind die Einheiten der Ergebnisse von Prüfungen der Werkstoffemissionen eigentlich so unterschiedlich?
Read moreGrenzwerte für Formaldehyd und Formaldehydabspaltern in Fahrzeugen
Read moreFREQUENTLY ASKED QUESTIONS ABOUT THE CHEMICAL RESISTANCE OF COATINGS
The test conditions, such as duration, concentration of chemicals and temperature, are defined individually according to customer requirements as well as industry-specific standards and manufacturer specifications. This allows real-life application scenarios to be precisely simulated.