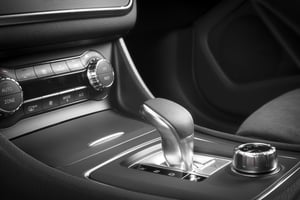
Fogging
Determination of the fogging behavior of materials used in vehicle interiors
FOGGING TEST IN THE
AUTOMOBILE INTERIOR
THE ROLE OF PHOTOGRAMMETRY IN CLIMATE TESTING IN THE AUTOMOTIVE INDUSTRY
The advanced requirements of the automotive industry make precise and reliable test methods indispensable. One of the key technologies for testing dimensionalstability under extreme climatic conditions is photogrammetry. It is used in the environmental simulation to accurately measurethree-dimensional deformations and in vehicle components. These tests help manufacturers and suppliers to optimize the quality and safety of their products and ensure that they can withstand even extreme conditions.
Fogging test methods
- DIN 75201-A (reflectrometric)
- DIN 75201-B (gravimetric)
- PV 3015 (Volkswagen)
- GMW 3235-A (General Motors Worldwide)
- PSA D45 1727
- and much more.
- What is photogrammetry?
- Use
- Devices and technologies
- TRITOP system
What is photogrammetry?
Photogrammetry is an optical measuring technique that enables the exact recording of deformations and changes in the geometry of vehicle parts caused by climatic influences such as temperature fluctuations or humidity.
Use of photogrammetry in environmental simulation:
- Detection of deformations: During climate testing, photogrammetry can document minute changes to the surfaces of vehicle components that occur due to extreme fluctuations in temperature and humidity.
- Non-contact measurements: Because photogrammetry is non-contact, it is ideal for testing sensitive or hard-to-reach components
- Documentation and traceability: The data obtained is documented and can later be used for further analysis and optimization. This is particularly valuable for quality assurance and product development.
Devices and technologies for photogrammetry in climate change testing:
- Digital measuring cameras: High-precision cameras record the smallest deformations and surface changes on vehicle parts, even at extreme temperatures.
- 3D scanning systems: Laser scanners create detailed models of the test parts to detect the smallest material changes.
Use of the TRITOP system for maximum precision
We use the high-precision optical photogrammetry system TRITOP for our inspections. TRITOP offers the following advantages:
- Highly accurate 3D measurements: Even for components with complex geometries, TRITOP delivers precise measurement results without the need for direct contact with the test parts.
- Flexible application options: The mobile system is ideally suited for use in various test environments
- Fast data acquisition: With TRITOP, we can record and analyze extensive data sets in the shortest possible time, enabling rapid verification of test results.
Fogging test methods
- DIN 75201-A (reflectrometric)
- DIN 75201-B (gravimetric)
- PV 3015 (Volkswagen)
- GMW 3235-A (General Motors Worldwide)
- PSA D45 1727
- and much more.
Are you looking for an exam? Standard? Specifications?
Accredited & certified tests
CONTACT OUR EXPERTS
Description. Lorem ipsum dolor sit amet, consetetur sadipscing elitr, sed diam nonumy eirmod tempor invidunt ut labore et
- Tab Title
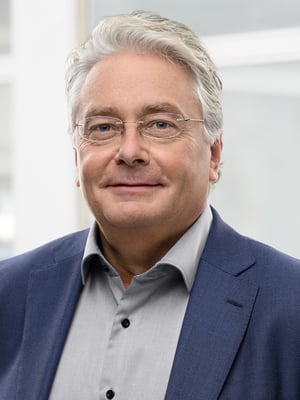
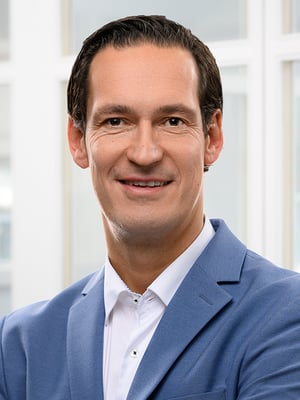
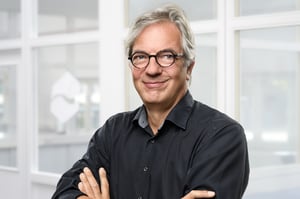
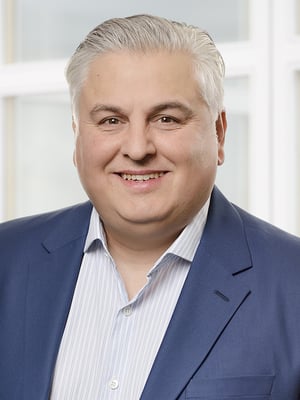
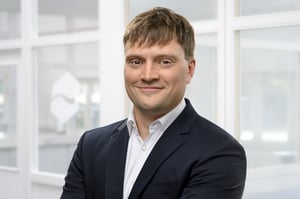
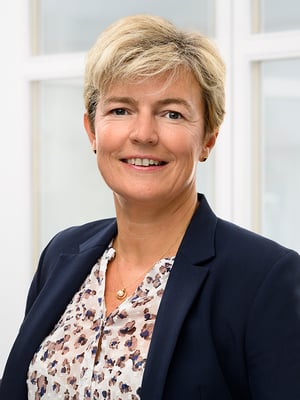
Frequently asked questions about the fogging test
The sample quantities required for a fogging test depend on the standard and the test method used. Here are the general guidelines:
1. standard DIN 75201 (type A and type B)
-
Type A (glass plate method):
A sample quantity of 10 cm² is typically required. The sample is placed on a heated plate in a sealed chamber and the volatiles released condense on a glass plate above. -
Type B (aluminum foil method):
Similar to type A, a sample volume of approximately 10 cm² is used. However, the volatile substances condense on a cooled aluminum foil.
2. standard ISO 6452 (international standard)
- Sample quantity:
Again, a sample size of about 10 cm² is typically required to evaluate the amount of volatiles released at elevated temperature.
3. other specific requirements
Depending on the specific requirements of the customer or OEM standards, sample quantities may vary. It is important to check the respective standards or test requirements carefully.
Method A - Reflectometric method:
- Principle: This method measures the change in reflectivity on a glass plate on which volatile components from the material sample are deposited.
- Procedure: A material sample is heated in a beaker while a glass plate above it is cooled to 21°C. The temperature difference causes the volatile components to condense on the glass plate. The reflectance index of the fogged glass plate is then measured to determine the amount of condensed material.
- Application: This method is particularly suitable for materials for which an exact determination of the optical fog effect is required.
Method B - Gravimetric method:
- Principle: This method measures the weight of condensed volatiles on an aluminum foil.
- Procedure: The material sample is heated in a beaker while an aluminum foil disc is cooled to 21°C. After 16 hours, the amount of condensed material on the foil is weighed.
- Application: This method is ideal for an accurate quantitative determination of the amount of condensed volatiles.
CONTACT US
ENVIRONMENTAL SIMULATION
FREQUENTLY ASKED QUESTIONS ABOUT PHOTOGRAMMETRY
- Interior trims
- Door panels
- seals
- Plastic components
- metal components
- and much more.