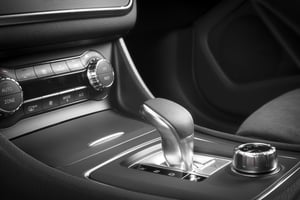
Fogging
Determination of the fogging behavior of materials used in vehicle interiors
FOGGING TEST IN THE
AUTOMOBILE INTERIOR
LONG-TERM EXPOSURE TO ENSURE MATERIAL RELIABILITY
As a testing service provider in the automotive sector, we are faced with the challenge of testing the durability and reliability of vehicle materials .
An important part of our work here is the analysis of material changes caused by outdoor weathering and long-term exposure tests in the laboratory. These tests help to ensure that the materials can withstand extreme outdoor conditions over long periods of time.
Importance of outdoor weathering
Outdoor weathering refers to the exposure of materials to natural environmental influences such as UV radiation, rain, temperature fluctuations and other atmospheric conditions. These influences can change the physical and chemical properties of the materials, which can have a negative impact on the functionality and appearance of vehicle components.
Long-term exposure test
Long-term exposure tests simulate these environmental conditions over a defined period of time. The tests are often carried out outdoors or in special climate chambers that mimic the various influencing factors in a controlled manner. The aim is to document the material changes and evaluate their effects on the performance and service life of the components.
Specific norms and standards that are taken into account:
Fogging test methods
- DIN 75201-A (reflectrometric)
- DIN 75201-B (gravimetric)
- PV 3015 (Volkswagen)
- GMW 3235-A (General Motors Worldwide)
- PSA D45 1727
- and much more.
Are you looking for an exam? Standard? Specifications?
Accredited & certified tests
CONTACT OUR EXPERTS
Description. Lorem ipsum dolor sit amet, consetetur sadipscing elitr, sed diam nonumy eirmod tempor invidunt ut labore et
- Tab Title
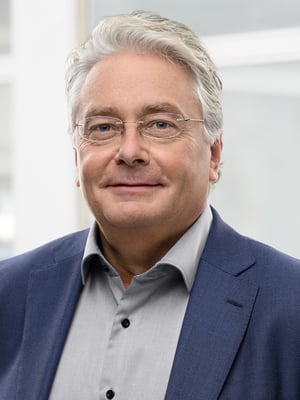
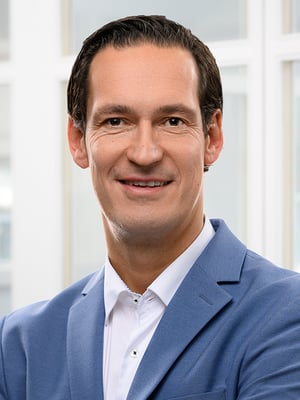
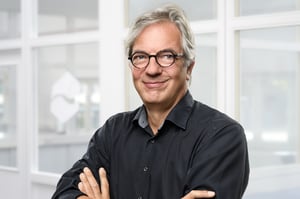
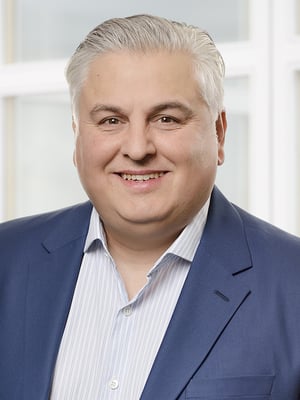
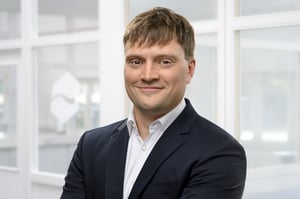
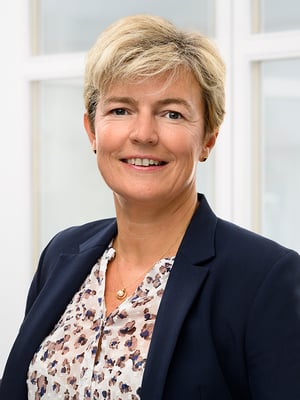
- ISO 4892
- SAE J1960
- ASTM G155
ISO 4892
SAE J1960
ASTM G155
Frequently asked questions about the fogging test
The sample quantities required for a fogging test depend on the standard and the test method used. Here are the general guidelines:
1. standard DIN 75201 (type A and type B)
-
Type A (glass plate method):
A sample quantity of 10 cm² is typically required. The sample is placed on a heated plate in a sealed chamber and the volatiles released condense on a glass plate above. -
Type B (aluminum foil method):
Similar to type A, a sample volume of approximately 10 cm² is used. However, the volatile substances condense on a cooled aluminum foil.
2. standard ISO 6452 (international standard)
- Sample quantity:
Again, a sample size of about 10 cm² is typically required to evaluate the amount of volatiles released at elevated temperature.
3. other specific requirements
Depending on the specific requirements of the customer or OEM standards, sample quantities may vary. It is important to check the respective standards or test requirements carefully.
Method A - Reflectometric method:
- Principle: This method measures the change in reflectivity on a glass plate on which volatile components from the material sample are deposited.
- Procedure: A material sample is heated in a beaker while a glass plate above it is cooled to 21°C. The temperature difference causes the volatile components to condense on the glass plate. The reflectance index of the fogged glass plate is then measured to determine the amount of condensed material.
- Application: This method is particularly suitable for materials for which an exact determination of the optical fog effect is required.
Method B - Gravimetric method:
- Principle: This method measures the weight of condensed volatiles on an aluminum foil.
- Procedure: The material sample is heated in a beaker while an aluminum foil disc is cooled to 21°C. After 16 hours, the amount of condensed material on the foil is weighed.
- Application: This method is ideal for an accurate quantitative determination of the amount of condensed volatiles.
CONTACT US
EMISSIONS & ODOR
Formaldehyd in Fahrzeugen: Herausforderungen für die Automobilindustrie
Read moreStellantis: Freigabe für Emissionsprüfungen erfolgreich (VIAQ)
Read moreVDA 277 vs. VDA 278: Was ist der Unterschied?
Read moreGeruchsunterschiede bei Polypropylen: Die Rolle von Faserverstärkung und Verarbeitungsparametern
Read moreWarum sind die Einheiten der Ergebnisse von Prüfungen der Werkstoffemissionen eigentlich so unterschiedlich?
Read moreGrenzwerte für Formaldehyd und Formaldehydabspaltern in Fahrzeugen
Read moreFREQUENTLY ASKED QUESTIONS ABOUT LONG-TERM EXPOSURE TESTS
The analysis of material changes includes various tests, such as mechanical tests, color and gloss measurements and chemical analyses. Changes such as cracking, discoloration or material degradation can indicate long-term exposure and must be documented in order to assess the integrity of the components.
IMAT-UVE IS ACCREDITED IN ACCORDANCE WITH DIN EN ISO/IEC 17025 AND ALSO HAS A
FLEXIBLE ACCREDITATION FOR THE FIELD OF ENVIRONMENTAL SIMULATION.
- Approval from Porsche for the DIN 75220 sun simulation method as part of the
Porsche specification PTL 8140 (for instrument panels, center consoles, complete vehicles) - BMW approval for the BMW PR 306.4 sun simulation method on interior equipment
- Further sun simulation tests, climate change and constant climate tests according to the requirements of other car manufacturers, as well as infrared tests on components according to Ford, GM/Opel, KIA/Hyundai specifications
- imat-uve is a member of the GUS/Society for Environmental Simulation
- GM/Opel approval for material testing with a focus on textiles and carpets
- Reference laboratory for upholstery and carpet testing
- Member of the VDA textile working group
- Emission testing according to VDA 278 for BMW, Daimler and GM/Opel, Porsche and Suzuki
- Member of various DIN committees
- OEM-certified test site in South Africa
- Our customers: Automotive manufacturers, system suppliers, parts suppliers, semi-finished product suppliers