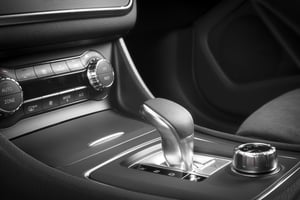
Fogging
Determination of the fogging behavior of materials used in vehicle interiors
FOGGING TEST IN THE
AUTOMOBILE INTERIOR
RESILIENCE AND STRENGTH ON THE TEST BENCH
Mechanical tests are a central component of quality assurance in the automotive industry. They are used to assess the load-bearing capacity, strength and durability of materials and components that are later installed in the vehicle. The most important tests include the tensile test, which examines the maximum load-bearing capacity and elongation of a material, and the impact strength test, which provides information on resistance to sudden impacts and loads.
In addition, compression and bending tests are carried out to test the structural integrity of components under realistic load scenarios. Hardness tests, which measure a material's resistance to penetration or wear, are also part of the essential procedures. These tests are essential to ensure that components such as plastic housings, metal connections or fastening elements can withstand the high safety and durability requirements in the automotive sector.
- Tensile and bending test
- Impact test
- Hardness test
- Print tests
Tensile and bending test
- Standard-compliant tests: Performance of tensile and bending tests in accordance with standards such as DIN EN ISO 527, DIN EN ISO 178 and DIN EN ISO 34.
- Variety of materials: Tensile tests on plastic test specimens, textiles and other flat goods to evaluate material strength and tear propagation properties.
- Bending properties: Analysis of the flexural strength of components, materials and vehicle components for load evaluation.
- Application safety: Evaluation of material elongation, breaking strength and elasticity for specific areas of application.
- Precise results: Validation of material properties for compliance with OEM specifications and international standards.
Impact test
- Standard-based tests: Performance of impact tests in accordance with DIN EN ISO 179, DIN EN ISO 180 and DIN 53435.
- Methods and temperature ranges: Impact tests such as Dynstat, Charpy and Izod with forces up to 100 kN, also at variable temperatures.
- Break resistance: Determination of energy absorption and material resistance to impact.
- Adaptation to requirements: Testing of components and materials that have to withstand extreme loads in the vehicle.
- Customer-specific tests: Adaptation of test procedures to specific requirements and specifications.
Hardness test
- Comprehensive hardness measurement: Measurements in accordance with DIN EN ISO 868 and DIN ISO 48 for Shore hardness (A, B, D) and IRHD hardness.
- Precise results: Rockwell and Vickers hardness measurements for different material types and applications.
- Material performance: Determination of surface strength and resistance to indentation and wear.
- Deformation resistance: Compression and tensile deformation residual tests in accordance with DIN ISO 815 and DIN ISO 2285 for elastomeric materials.
- Wide range of applications: Hardness analyses to ensure material stability under real application conditions.
Print tests
- Standard-compliant tests: Carrying out compression tests in accordance with DIN ISO 815 with variable compression specimens.
- Material deformation: Analysis of the compression set and the resilience of elastic materials.
- Load testing: Evaluation of the tensile deformation residual according to DIN ISO 2285 for materials under mechanical stress.
- Wide range of applications: Tests on components and materials that have to withstand high pressures.
- Validation of components: Ensuring material suitability for use in demanding vehicle environments.
Test methods
- DIN EN ISO 527-2
- DIN EN ISO 178
- DIN EN ISO 179-1
- DIN 53435
- DIN ISO 7619-1
- and much more.
Fogging test methods
- DIN 75201-A (reflectrometric)
- DIN 75201-B (gravimetric)
- PV 3015 (Volkswagen)
- GMW 3235-A (General Motors Worldwide)
- PSA D45 1727
- and much more.
Are you looking for an exam? Standard? Specifications?
Accredited & certified tests
CONTACT OUR EXPERTS
Description. Lorem ipsum dolor sit amet, consetetur sadipscing elitr, sed diam nonumy eirmod tempor invidunt ut labore et
- Tab Title
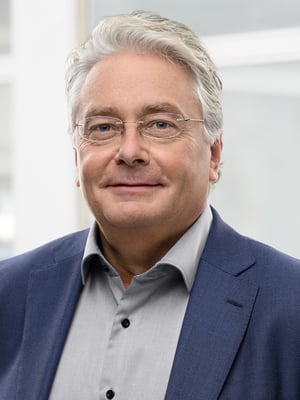
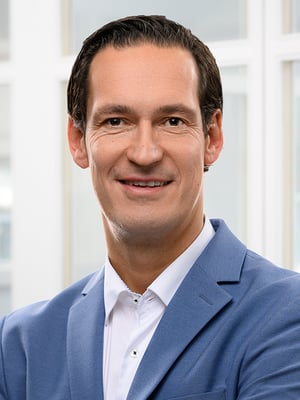
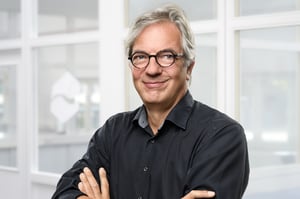
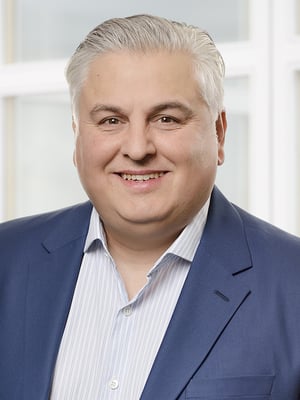
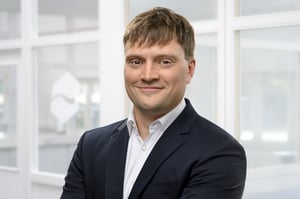
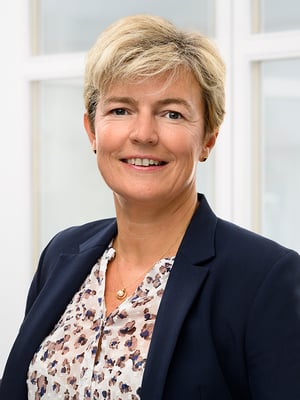
Frequently asked questions about the fogging test
The sample quantities required for a fogging test depend on the standard and the test method used. Here are the general guidelines:
1. standard DIN 75201 (type A and type B)
-
Type A (glass plate method):
A sample quantity of 10 cm² is typically required. The sample is placed on a heated plate in a sealed chamber and the volatiles released condense on a glass plate above. -
Type B (aluminum foil method):
Similar to type A, a sample volume of approximately 10 cm² is used. However, the volatile substances condense on a cooled aluminum foil.
2. standard ISO 6452 (international standard)
- Sample quantity:
Again, a sample size of about 10 cm² is typically required to evaluate the amount of volatiles released at elevated temperature.
3. other specific requirements
Depending on the specific requirements of the customer or OEM standards, sample quantities may vary. It is important to check the respective standards or test requirements carefully.
Method A - Reflectometric method:
- Principle: This method measures the change in reflectivity on a glass plate on which volatile components from the material sample are deposited.
- Procedure: A material sample is heated in a beaker while a glass plate above it is cooled to 21°C. The temperature difference causes the volatile components to condense on the glass plate. The reflectance index of the fogged glass plate is then measured to determine the amount of condensed material.
- Application: This method is particularly suitable for materials for which an exact determination of the optical fog effect is required.
Method B - Gravimetric method:
- Principle: This method measures the weight of condensed volatiles on an aluminum foil.
- Procedure: The material sample is heated in a beaker while an aluminum foil disc is cooled to 21°C. After 16 hours, the amount of condensed material on the foil is weighed.
- Application: This method is ideal for an accurate quantitative determination of the amount of condensed volatiles.
CONTACT US
MATERIAL TESTS
Medienbeständigkeit in der Automobilbranche
Read moreWebinar Insights: Grundlagen der Dickenmessung bei Textilien
Read moreOptimierung der Automobilsitze: Nahtqualität im Fokus
Read moreMace Snag Prüfung: Qualitätssicherung bei Automobiltextilien
Read moreWie Automobilzulieferer die richtigen Prüfnormen finden
Read moreWas versteht man unter Umweltsimulation im automobilen Kontext?
Read moreFREQUENTLY ASKED QUESTIONS ABOUT MECHANICAL TESTING
Yes, imat-uve is accredited, released and approved for various tests.
Disclaimer
The information provided is based on many years of experience and is for general information purposes only. No guarantee is given for the correctness, completeness or topicality of the contents. Warranty claims cannot be derived from this information and the rights of third parties remain unaffected. Details on sampling, sample preparation, test equipment, test methods and the performance and evaluation of test results can be found in the latest versions of the underlying standards.