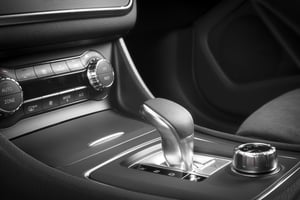
Fogging
Determination of the fogging behavior of materials used in vehicle interiors
FOGGING TEST IN THE
AUTOMOBILE INTERIOR
SIGNIFICANCE OF THE ELECTRICAL LOAD IN THE UTILIZATION PHASE
Vehicles are exposed to extreme conditions during the use phase. Temperature fluctuations, vibrations, humidity and electromagnetic interference affect the performance and longevity of individual components. Precise simulation of these loads makes it possible to identify potential failures at an early stage and increase product reliability.
The simulation of electrical stress over the life cycle of vehicle components is crucial for OEMs and suppliers to ensure the reliability and safety of their products. As a testing service provider, we offer specialized solutions to address the challenges and requirements in the critical use phase of individual components.
- 01 Ambient conditions
- 02 Vibrations and mechanical loads
Ambient conditions
Various standards, such as VW 80000 or LV124,specify which climatic conditions must be taken into account during the tests. This includes extreme temperatures and high humidity, which affect the electrical properties of the components.
Vibrations and mechanical loads
Technologies and methods for simulation
Fogging test methods
- DIN 75201-A (reflectrometric)
- DIN 75201-B (gravimetric)
- PV 3015 (Volkswagen)
- GMW 3235-A (General Motors Worldwide)
- PSA D45 1727
- and much more.
Are you looking for an exam? Standard? Specifications?
Accredited & certified tests
CONTACT OUR EXPERTS
Description. Lorem ipsum dolor sit amet, consetetur sadipscing elitr, sed diam nonumy eirmod tempor invidunt ut labore et
- Tab Title
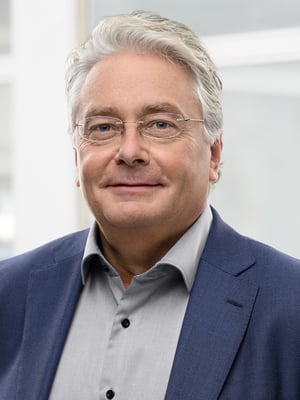
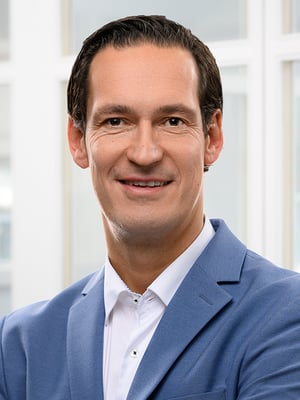
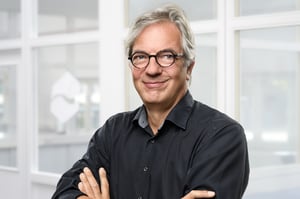
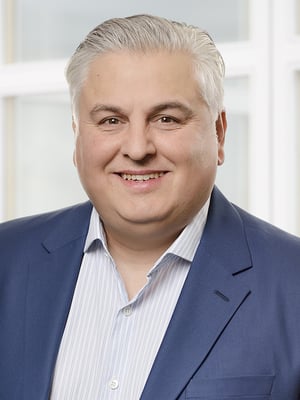
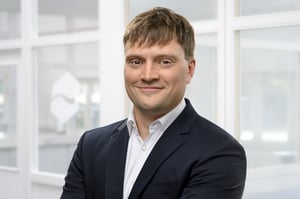
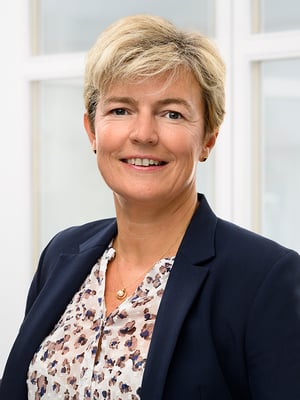
TECHNOLOGIES AND METHODS FOR SIMULATION
In order to realistically simulate the electrical loads and meet the corresponding requirements, we rely on state-of-the-art technologies and test methods :
- Multiphysics simulation: this technology enables the simultaneous consideration of electrical, thermal and mechanical phenomena. This is crucial in order to understand the complex interactions and meet the standard requirements.
- Service life modeling: By using service life models, we can predict the expected service life of components under realistic operating conditions, which also takes into account the requirements of the standard.
- Cyclic load tests: These tests simulate the repeated loads that components experience in vehicle operation and are important for identifying potential weak points in the design at an early stage.
The implementation of electrical load simulations offers numerous advantages:
- Early identification of weak points: Simulation allows potential problems to be identified early before they occur in real-world use. This helps to avoid costly recalls and repairs.
- Optimization of product reliability: The analysis of simulation results enables targeted adjustments that increase the service life and performance of the products.
- Compliance with standards: Our tests ensure conformity with current standards, guaranteeing product quality and safety.
- Cost efficiency: By reducing the need for extensive physical testing, development costs can be lowered while product quality is improved.
Frequently asked questions about the fogging test
The sample quantities required for a fogging test depend on the standard and the test method used. Here are the general guidelines:
1. standard DIN 75201 (type A and type B)
-
Type A (glass plate method):
A sample quantity of 10 cm² is typically required. The sample is placed on a heated plate in a sealed chamber and the volatiles released condense on a glass plate above. -
Type B (aluminum foil method):
Similar to type A, a sample volume of approximately 10 cm² is used. However, the volatile substances condense on a cooled aluminum foil.
2. standard ISO 6452 (international standard)
- Sample quantity:
Again, a sample size of about 10 cm² is typically required to evaluate the amount of volatiles released at elevated temperature.
3. other specific requirements
Depending on the specific requirements of the customer or OEM standards, sample quantities may vary. It is important to check the respective standards or test requirements carefully.
Method A - Reflectometric method:
- Principle: This method measures the change in reflectivity on a glass plate on which volatile components from the material sample are deposited.
- Procedure: A material sample is heated in a beaker while a glass plate above it is cooled to 21°C. The temperature difference causes the volatile components to condense on the glass plate. The reflectance index of the fogged glass plate is then measured to determine the amount of condensed material.
- Application: This method is particularly suitable for materials for which an exact determination of the optical fog effect is required.
Method B - Gravimetric method:
- Principle: This method measures the weight of condensed volatiles on an aluminum foil.
- Procedure: The material sample is heated in a beaker while an aluminum foil disc is cooled to 21°C. After 16 hours, the amount of condensed material on the foil is weighed.
- Application: This method is ideal for an accurate quantitative determination of the amount of condensed volatiles.
EMISSIONS & ODOR
Formaldehyd in Fahrzeugen: Herausforderungen für die Automobilindustrie
Read moreStellantis: Freigabe für Emissionsprüfungen erfolgreich (VIAQ)
Read moreVDA 277 vs. VDA 278: Was ist der Unterschied?
Read moreGeruchsunterschiede bei Polypropylen: Die Rolle von Faserverstärkung und Verarbeitungsparametern
Read moreWarum sind die Einheiten der Ergebnisse von Prüfungen der Werkstoffemissionen eigentlich so unterschiedlich?
Read moreGrenzwerte für Formaldehyd und Formaldehydabspaltern in Fahrzeugen
Read moreFREQUENTLY ASKED QUESTIONS ABOUT SERVICE LIFE TESTING
- Early identification of weak points
- Optimization of product reliability
- Compliance with standards
- Cost efficiency