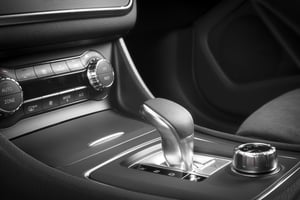
Fogging
Bestimmung des Foggingverhaltens von Werkstoffen der Kraftfahrzeug-Innenausstattung
FOGGING-PRÜFUNG IM
AUTOMOBIL-INNENRAUM
STEINSCHLAGTESTS: BELASTBARKEIT UND SCHUTZ FÜR LANGLEBIGE LACKIERUNGEN
Steinschlagtests sind eine wichtige Methode zur Bewertung der Widerstandsfähigkeit von Lackierungen, insbesondere im Automobilbereich, wo Oberflächen täglichen Belastungen durch aufgewirbelte Steine und Schmutzpartikel ausgesetzt sind. Diese Tests simulieren realistische Szenarien, bei denen mechanische Einflüsse gezielt nachgestellt werden, um die Belastbarkeit von lackierten Fahrzeugteilen wie Stoßfängern oder Bodenverkleidungen zu prüfen. Ziel ist es, Schwachstellen frühzeitig zu erkennen und die Qualität der Beschichtungen nachhaltig zu verbessern, damit diese auch unter anspruchsvollen Bedingungen langlebig und funktional bleiben.
Nach der DIN EN ISO 20567-1 wird genormtes Hartgussgranulat unter definiertem Druck und Winkel auf die Prüflinge geschossen, um die reale Beanspruchung durch Straßenschmutz nachzubilden. Der Beschuss erfolgt mit variierbarem Druck, da die Geschwindigkeit des Granulats nicht direkt in km/h einstellbar ist. Die Prüfanlage wird regelmäßig kalibriert, und das Granulat routinemäßig ausgetauscht, um reproduzierbare Ergebnisse sicherzustellen. Parameter wie Korngröße, Beschussmenge, Winkel und Druck werden an die jeweiligen Norm- und Herstellervorgaben angepasst.
Nach Abschluss der Tests wird das Schadensausmaß visuell bewertet und dokumentiert, wobei auch die betroffenen Schichten berücksichtigt werden. Für aussagekräftige Ergebnisse ist es erforderlich, dass die Proben in sauberem und unbeschädigtem Zustand geliefert werden. Eine stoßfeste Verpackung schützt die Proben während des Transports, und Begleitdokumente mit Details zur Beschichtung sowie zu den Schichtinformationen erleichtern die Testvorbereitung.
Die Prüfparameter umfassen den Druck, die Korngröße des Granulats, den Beschusswinkel und die Anzahl der Proben. Mindestens fünf Musterteile sind pro Testreihe erforderlich, wobei zusätzliche Muster für Vergleichstests empfohlen werden. Der Versand erfolgt an unsere Prüfstelle in stoßsicherer Verpackung, begleitet von Informationen zur Beschichtung und Materialzusammensetzung, um eine umfassende und präzise Analyse zu gewährleisten. Unsere professionellen Steinschlagtests bieten Ihnen verlässliche Ergebnisse und stärken das Vertrauen in die Qualität Ihrer Beschichtungen.
Steinschlag- Prüfmethoden
- BMW AA-0079
- BMW AA-0264
- Fiat 50488/01
- Ford FLTM BI 157-06
- Nissan NES M0007 § 28 / SAE J400
- VW PV 1217
- VW PV 3.14.4
- VinFast VFDST00044000
- Volvo VCS 1024,71359
- u.v.m.
Fogging-Prüfmethoden
- DIN 75201-A (reflektrometrisch)
- DIN 75201-B (gravimetrisch)
- PV 3015 (Volkswagen)
- GMW 3235-A (General Motors Worldwide)
- PSA D45 1727
- u.v.m.
Sie suchen nach einer Prüfung? Norm? Lastenheft?
Akkreditierte & zertifizierte Prüfungen
KONTAKTIEREN SIE UNSERE EXPERTEN
Description. Lorem ipsum dolor sit amet, consetetur sadipscing elitr, sed diam nonumy eirmod tempor invidunt ut labore et
- Tab Title
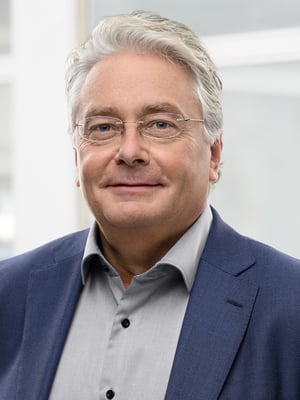
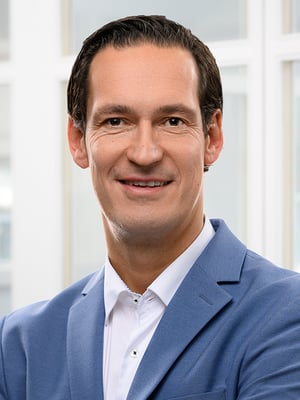
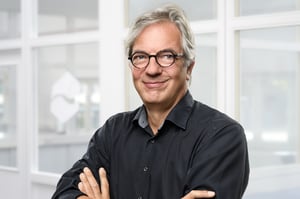
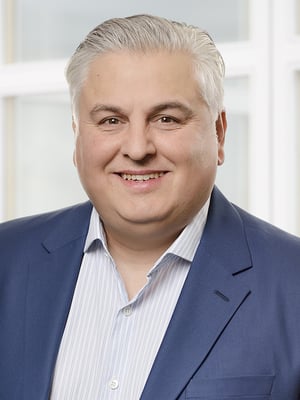
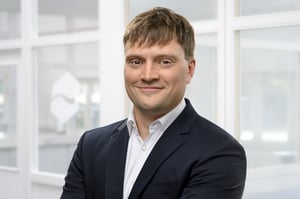
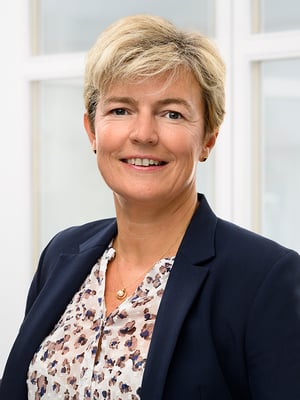
- 01 Zweck der Steinschlagtests
- 02 Prüfdurchführung
Zweck der Steinschlagtests
- Bewertung der Widerstandsfähigkeit: Überprüfung, wie Lackierungen mechanischen Einflüssen wie aufgewirbelten Steinen und Straßenschmutz standhalten.
- Erkennung von Schwachstellen: Identifikation von Beschichtungsmängeln, um die Qualität frühzeitig zu verbessern.
- Simulation realistischer Bedingungen: Nachstellung alltäglicher Belastungen gemäß DIN EN ISO 20567-1 für realitätsnahe Ergebnisse.
- Qualitätssicherung: Sicherstellung der Langlebigkeit und Schutzfunktion von Fahrzeuglackierungen.
- Einhaltung von Normen und Vorgaben: Prüfung der Lackierungen auf Basis herstellerspezifischer Anforderungen und internationaler Standards.
Prüfdurchführung
Die Steinschlagtests werden nach der Norm DIN EN ISO 20567-1 durchgeführt, um realistische Beanspruchungen durch aufgewirbelte Steine und Straßenschmutz zu simulieren. Dabei wird genormtes Hartgussgranulat unter definiertem Druck und Winkel auf die zu prüfenden Proben geschossen. Die Prüfanlage ermöglicht es, den Druck und damit die Geschwindigkeit des Granulats zu variieren, da die Beschussgeschwindigkeit nicht direkt in km/h einstellbar ist. Dies gewährleistet eine präzise Anpassung der Testparameter an reale Belastungssituationen.
Um reproduzierbare Ergebnisse zu erzielen, wird die Prüfanlage regelmäßig kalibriert und das Granulat routinemäßig ausgetauscht. Je nach Norm- oder Herstellervorgaben können Parameter wie Korngröße, Beschussmenge, Winkel und Druck flexibel angepasst werden.
Nach Abschluss der Tests erfolgt eine visuelle Bewertung des Schadensausmaßes. Dabei werden die betroffenen Schichten dokumentiert und die Ergebnisse gemäß den normativen Vorgaben analysiert. Für eine zuverlässige Durchführung ist es wichtig, dass die Proben in sauberem und unbeschädigtem Zustand geliefert werden. Der Transport erfolgt in stoßsicherer Verpackung, begleitet von Begleitdokumenten mit Angaben zu Beschichtung und Schichtinformationen. So wird sichergestellt, dass alle relevanten Details in die Prüfparameter einfließen und eine präzise Analyse möglich ist.
WEITERE PRÜFUNGEN UND SERVICE
Vertrauen Sie auf über 30 Jahre Automotive-Testing Kompetenz
Häufig gestellte Fragen zur Fogging-Prüfung
Für eine Fogging-Prüfung sind die benötigten Probenmengen abhängig von der Norm und dem verwendeten Prüfverfahren. Hier sind die allgemeinen Richtlinien:
1. Norm DIN 75201 (Typ A und Typ B)
-
Typ A (Glasplattenmethode):
Es wird typischerweise eine Probenmenge von 10 cm² benötigt. Die Probe wird auf einer beheizten Platte in einer verschlossenen Kammer platziert, und die freigesetzten flüchtigen Stoffe kondensieren auf einer darüber befindlichen Glasplatte. -
Typ B (Aluminiumfolienmethode):
Ähnlich wie bei Typ A wird eine Probenmenge von etwa 10 cm² verwendet. Die flüchtigen Stoffe kondensieren hier jedoch auf einer gekühlten Aluminiumfolie.
2. Norm ISO 6452 (internationale Norm)
- Probenmenge:
Auch hier wird typischerweise eine Probenmenge von etwa 10 cm² benötigt, um die Menge der flüchtigen Stoffe, die bei erhöhter Temperatur freigesetzt werden, zu bewerten.
3. Weitere spezifische Anforderungen
Je nach spezifischen Anforderungen des Kunden oder der OEM-Normen können die Probenmengen variieren. Es ist wichtig, die jeweiligen Normen oder Prüfanforderungen genau zu prüfen.
Methode A - Reflektometrische Methode:
- Prinzip: Diese Methode misst die Änderung des Reflexionsvermögens auf einer Glasplatte, auf der sich flüchtige Bestandteile aus der Materialprobe absetzen.
- Verfahren: Eine Materialprobe wird in einem Becherglas erhitzt, während eine darüberliegende Glasplatte auf 21°C gekühlt wird. Durch die Temperaturdifferenz kondensieren die flüchtigen Bestandteile auf der Glasplatte. Anschließend wird der Reflexionsindex der beschlagenen Glasplatte gemessen, um die Menge des kondensierten Materials zu bestimmen.
- Anwendungsbereich: Diese Methode eignet sich besonders gut für Materialien, bei denen eine genaue Bestimmung des optischen Nebeleffekts gewünscht ist.
Methode B - Gravimetrische Methode:
- Prinzip: Diese Methode misst das Gewicht der kondensierten flüchtigen Bestandteile auf einer Aluminiumfolie.
- Verfahren: Die Materialprobe wird in einem Becherglas erhitzt, während eine Aluminiumfolienscheibe auf 21°C gekühlt wird. Nach 16 Stunden wird die Menge des kondensierten Materials auf der Folie gewogen.
- Anwendungsbereich: Diese Methode ist ideal für eine genaue quantitative Bestimmung der Menge an kondensierten flüchtigen Bestandteilen.
JETZT KONTAKT AUFNEHMEN
KORROSION
Formaldehyd in Fahrzeugen: Herausforderungen für die Automobilindustrie
WeiterlesenStellantis: Freigabe für Emissionsprüfungen erfolgreich (VIAQ)
WeiterlesenVDA 277 vs. VDA 278: Was ist der Unterschied?
WeiterlesenGeruchsunterschiede bei Polypropylen: Die Rolle von Faserverstärkung und Verarbeitungsparametern
WeiterlesenWarum sind die Einheiten der Ergebnisse von Prüfungen der Werkstoffemissionen eigentlich so unterschiedlich?
WeiterlesenGrenzwerte für Formaldehyd und Formaldehydabspaltern in Fahrzeugen
WeiterlesenHÄUFIG GESTELLTE FRAGEN ZU STEINSCHLAGTESTS
Die Proben sollten sauber, frei von Beschädigungen und Verunreinigungen geliefert werden. Eine stoßsichere Verpackung schützt sie vor Transportschäden. Angaben zu Lacktyp, Schichtsystem und Beschichtungsprozess sind notwendig, um die Prüfparameter optimal festzulegen.