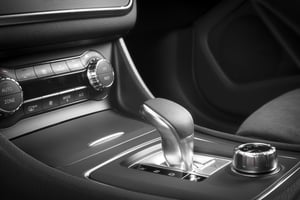
Fogging
Determination of the fogging behavior of materials used in vehicle interiors
FOGGING TEST IN THE
AUTOMOBILE INTERIOR
EMISSION CHAMBER TESTS FOR THE PROTECTION OF MATERIALS AND COMPONENTS OF THE VEHICLE INTERIOR
Emission tests on material samples, materials and small parts provide valuable information on their emission behavior. They enable a qualitative assessment of the release potential of undesirable substances. In complex parts and components, however, individual materials are often covered or even stuck together. In addition, the non-comparable production conditions ensure that the tests for material qualification are not sufficient for an assessment of the complete components. The use of emission chamber tests is essential for this, as they allow the components to be validated in their entirety. In contrast to material tests (such as VDA 277 and VDA 278), emission chamber tests allow significantly better conclusions to be drawn about possible contributions to air pollution in the complete vehicle and thus aim to validate parts and components .
Under defined test conditions that simulate realistic stress, the VOCs from the components accumulate in the air of the test chamber. Using a flame ionization detector (FID), the concentration of VOCs in the air of the test chamber is determined and recorded directly as a total value during the entire test. Identification and quantitative determination of the VOCs enables samples to be taken from collection media for subsequent analysis in the laboratory. As far as possible, universal adsorbents are used as collection media for the VOC overview analysis (also known as "VOC screening"). Specially selected collection media can be used to analyze specific VOCs that are not adequately captured by the universal media. In addition, our professionally trained test persons evaluate the test room air for odor .
Especially for materials and semi-finished products with larger quantities used per vehicle (e.g. foams, textiles or artificial leather films), the extended analysis options of the chamber tests and the improved sensitivity of the measurement are used to qualify the materials and composite materials.
The use of state-of-the-art test chambers at imat and our high quality standards guarantee you precise and meaningful results. You benefit from our many years of expertise in the field of emission chamber testing through practical recommendations for material selection and optimization of your products. Our aim is to strengthen your innovative power and support you in the development of safe, environmentally friendly and high-quality vehicles that meet your customers' expectations.
Fogging test methods
- DIN 75201-A (reflectrometric)
- DIN 75201-B (gravimetric)
- PV 3015 (Volkswagen)
- GMW 3235-A (General Motors Worldwide)
- PSA D45 1727
- and much more.
Are you looking for an exam? Standard? Specifications?
Accredited & certified tests
CONTACT OUR EXPERTS
Description. Lorem ipsum dolor sit amet, consetetur sadipscing elitr, sed diam nonumy eirmod tempor invidunt ut labore et
- Tab Title
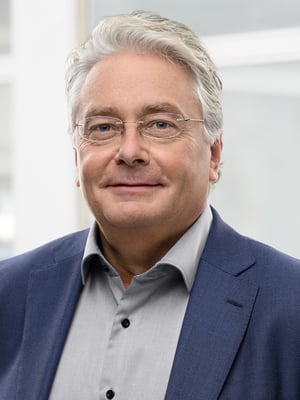
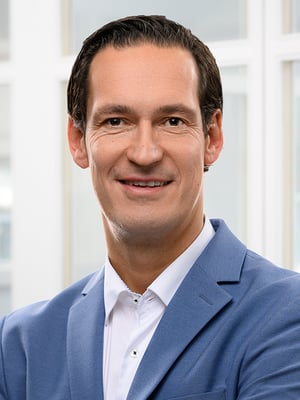
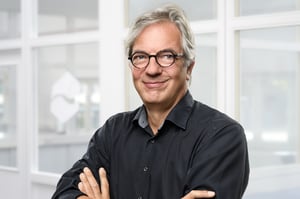
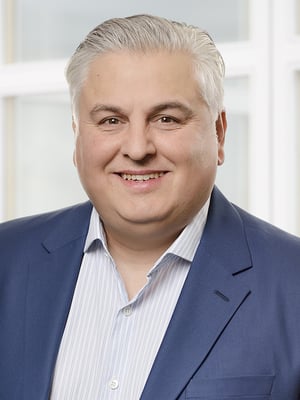
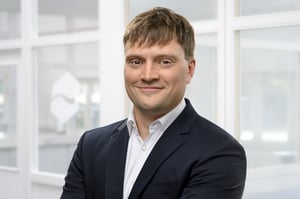
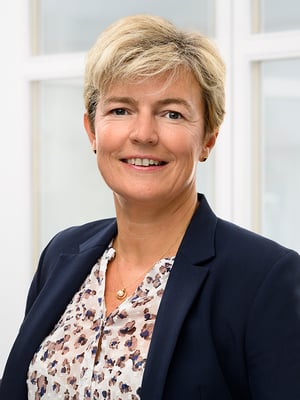
- 01 Purpose of the emission chamber test
Purpose of the emission chamber test
- Validation of complete components: Emission chamber testing enables precise evaluation of parts and components in their complete form, especially when material testing is not sufficient.
- Evaluation of emission behavior: The tests provide comprehensive insights into the release of undesirable substances and their influence on indoor air quality.
- Extended analysis options: Specific collection media and VOC screening can be used to precisely identify and quantify individual substances.
- Simulation of realistic conditions: Defined test conditions simulate the actual stress on the materials in the vehicle.
- Practical optimization: The results support material selection and product optimization in order to develop environmentally friendly and high-quality vehicles.
Frequently asked questions about the fogging test
The sample quantities required for a fogging test depend on the standard and the test method used. Here are the general guidelines:
1. standard DIN 75201 (type A and type B)
-
Type A (glass plate method):
A sample quantity of 10 cm² is typically required. The sample is placed on a heated plate in a sealed chamber and the volatiles released condense on a glass plate above. -
Type B (aluminum foil method):
Similar to type A, a sample volume of approximately 10 cm² is used. However, the volatile substances condense on a cooled aluminum foil.
2. standard ISO 6452 (international standard)
- Sample quantity:
Again, a sample size of about 10 cm² is typically required to evaluate the amount of volatiles released at elevated temperature.
3. other specific requirements
Depending on the specific requirements of the customer or OEM standards, sample quantities may vary. It is important to check the respective standards or test requirements carefully.
Method A - Reflectometric method:
- Principle: This method measures the change in reflectivity on a glass plate on which volatile components from the material sample are deposited.
- Procedure: A material sample is heated in a beaker while a glass plate above it is cooled to 21°C. The temperature difference causes the volatile components to condense on the glass plate. The reflectance index of the fogged glass plate is then measured to determine the amount of condensed material.
- Application: This method is particularly suitable for materials for which an exact determination of the optical fog effect is required.
Method B - Gravimetric method:
- Principle: This method measures the weight of condensed volatiles on an aluminum foil.
- Procedure: The material sample is heated in a beaker while an aluminum foil disc is cooled to 21°C. After 16 hours, the amount of condensed material on the foil is weighed.
- Application: This method is ideal for an accurate quantitative determination of the amount of condensed volatiles.
CONTACT US
EMISSIONS & ODOR
Formaldehyd in Fahrzeugen: Herausforderungen für die Automobilindustrie
Read moreStellantis: Freigabe für Emissionsprüfungen erfolgreich (VIAQ)
Read moreVDA 277 vs. VDA 278: Was ist der Unterschied?
Read moreGeruchsunterschiede bei Polypropylen: Die Rolle von Faserverstärkung und Verarbeitungsparametern
Read moreWarum sind die Einheiten der Ergebnisse von Prüfungen der Werkstoffemissionen eigentlich so unterschiedlich?
Read moreGrenzwerte für Formaldehyd und Formaldehydabspaltern in Fahrzeugen
Read moreFREQUENTLY ASKED QUESTIONS ABOUT EMISSION CHAMBER TESTING
During the test, the volatile organic compounds (VOCs) from the materials accumulate in the test chamber air. The concentration of VOCs is measured as a total value using a flame ionization detector (FID). In addition, samples are taken for laboratory analysis in order to identify and quantify specific VOCs.