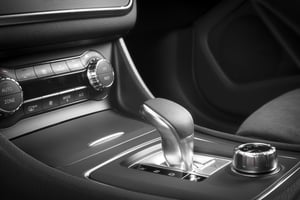
Vernebeln
Bestimmung des Fogging-Verhaltens von Materialien für den Fahrzeuginnenraum
FOGGING-TEST IM
AUTOMOBILINNENRAUM
EFFEKTIVE FOGGING-TESTS ZUR ÜBERPRÜFUNG DER EIGNUNG VON MATERIALIEN FÜR SCHEIBENNAHE ANWENDUNGEN
Fogging-Test zur Prüfung auf Ausgasung schwerflüchtiger organischer Verbindungen aus Kunststoffen und anderen Materialien. Überprüfen Sie Ihr Material mit präzisen Testmethoden auf die Bildung unerwünschter Ablagerungen auf Oberflächen wie z. B. Windschutzscheiben. Erfahren Sie jetzt mehr!
Fogging ist ein Phänomen, das im Fahrzeuginnenraum auftritt, wenn schwerflüchtige organische Verbindungen (FOG) aus Kunststoffen, Textilien, Schaumstoffen oder anderen nicht-metallischen Materialien entweichen und auf kälteren Oberflächen, wie z. B. der Windschutzscheibe, kondensieren. Diese Verbindungen kondensieren und hinterlassen eine oft klebrige, fettige Schicht, die die Sicht beeinträchtigen kann - ein Effekt, der als "Fogging" bekannt ist. Dieses Problem ist nicht nur optisch störend, sondern kann auch die Fahrsicherheit erheblich beeinträchtigen, insbesondere bei schlechtem Wetter oder nachts, wenn eine klare Sicht durch die Windschutzscheibe unerlässlich ist.
Um die Beschlagseigenschaften von Materialien im Fahrzeuginnenraum zu beurteilen, wird der so genannte Fogging-Test durchgeführt. Bei diesem Test wird das zu prüfende Material erhitzt, wodurch flüchtige Bestandteile entweichen. Diese kondensieren dann an einer kälteren Oberfläche und werden anschließend quantifiziert. Es gibt zwei Hauptmethoden, von denen in der Regel eine verwendet wird :
Gravimetrische Methode: Sie misst die Gewichtszunahme, die durch die Kondensation der flüchtigen Bestandteile auf einer zuvor gewogenen Platte entsteht. Diese Methode liefert genaue Informationen über die Menge der ausgasenden Verbindungen und gibt den Vernebelungswert als Masse in Milligramm an. Typische Ergebnisse liegen im Bereich von 2 bis 5 mg, wobei Werte unter 2 mg als besonders gut gelten.
Reflektometrische Methode: Bei dieser Methode wird die Lichtreflexion der Oberfläche gemessen, nachdem sich die kondensierten Verbindungen dort niedergeschlagen haben. Ein hoher Reflexionswert, ausgedrückt als Prozentsatz, zeigt an, dass die Oberfläche weniger vom Beschlagen betroffen ist. Ein Reflexionsgrad von über 80 % wird als optimal angesehen.
Der Fogging-Test ist entscheidend, um die Qualität und Sicherheit von Materialien im Fahrzeuginnenraum zu gewährleisten. Die Hersteller von Fahrzeugteilen und -materialien nutzen diesen Test, um sicherzustellen, dass ihre Produkte die strengen Anforderungen an emissionsarme Materialien erfüllen und dass keine potenziellen Sicherheitsrisiken aufgrund einer verminderten Sicht im Fahrzeug bestehen.
Vor allem in der Automobilindustrie ist die Prüfung auf Beschlag ein wesentlicher Schritt, um die Anforderungen der verschiedenen Automobilhersteller zu erfüllen. Viele führende Automobilhersteller wie die BMW Group, Daimler, Volkswagen und Ford verwenden die Methode, um sicherzustellen, dass die verwendeten Materialien keine unerwünschten Ausgasungen verursachen.
Darüber hinaus hilft der Fogging-Test nicht nur, optische Probleme zu vermeiden, sondern unterstützt auch die Einhaltung von Umwelt- und Gesundheitsvorschriften. Denn der Test ermöglicht es, emissionsarme und damit umweltfreundlichere Materialien zu identifizieren und einzusetzen.
Fogging
Prüfmethoden
- BMW Gruppe: DIN 75201
- Mercedes-Benz (ehemals Daimler): DIN 75201
- Fiat Chrysler Automobiles: SAE J 1756
- Ford: SAE J 1756
- General Motors: GMW 3235
- Jaguar/Land Rover: SAE J 1756
- Porsche: DIN 75201
- Volkswagen Konzern: PV 3015
- Volvo: VCS 1027,2719
- Toyota: TSM 0503 G
- Renault: D45 1725
- PSA (Peugeot / Citroën): D45 1725
- und viele mehr.
Fogging-Testmethoden
- DIN 75201-A (reflektrometrisch)
- DIN 75201-B (gravimetrisch)
- PV 3015 (Volkswagen)
- GMW 3235-A (General Motors weltweit)
- PSA D45 1727
- und vieles mehr.
Suchen Sie nach einer Prüfung? Norm? Spezifikationen?
Akkreditierte und zertifizierte Tests
KONTAKT ZU UNSEREN EXPERTEN
Beschreibung. Lorem ipsum dolor sit amet, consetetur sadipscing elitr, sed diam nonumy eirmod tempor invidunt ut labore et
- Registerkarte Titel
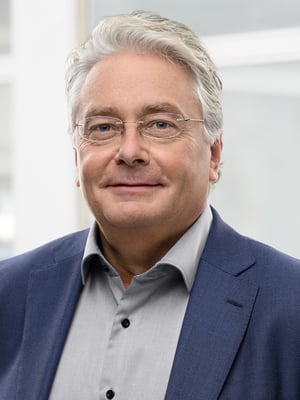
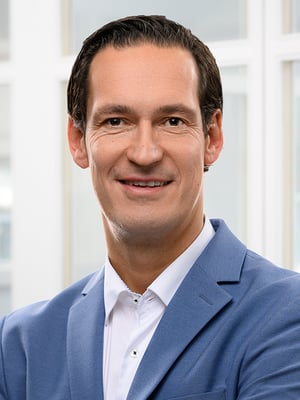
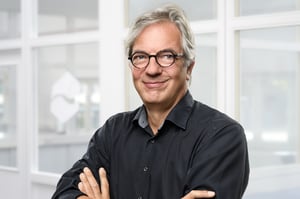
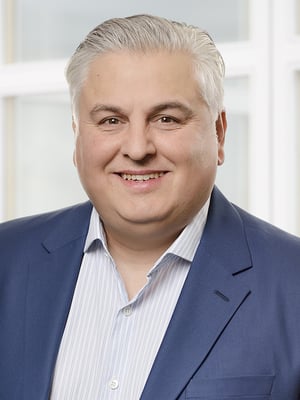
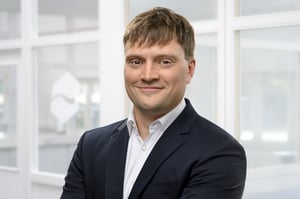
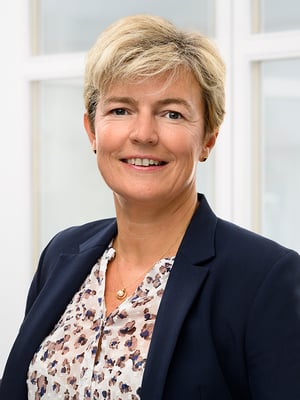
- 01 Zweck des Foggings
- 02 Testmethoden
Zweck des Foggings
- Vermeidung von Sichtproblemen: Der Beschlagtest hilft dabei, Materialien zu identifizieren, die unerwünschtes Beschlagen auf Oberflächen wie Windschutzscheiben verursachen, um klare Sicht und Fahrsicherheit zu gewährleisten.
- Bewertung der Beschlagseigenschaften: Präzise Tests messen und bewerten das Austreten von schwerflüchtigen organischen Verbindungen (FOG) aus Materialien.
- Einhaltung von Qualitäts- und Sicherheitsstandards: Hersteller nutzen den Fogging-Test, um sicherzustellen, dass ihre Materialien die Anforderungen an emissionsarme Produkte und die Spezifikationen führender Automobilhersteller erfüllen.
- Unterstützung von Umwelt- und Gesundheitsvorschriften: Die Methode ermöglicht die Identifizierung umweltfreundlicherer Materialien, die weniger schädliche Emissionen erzeugen.
- Präzise Messmethoden: Die gravimetrische und die reflektometrische Methode liefern detaillierte Ergebnisse zur Menge und Sichtbarkeit der kondensierten Verbindungen.
Testmethoden
- Fogging-Test (gravimetrisch )
- Normen: DIN 75201-B, ISO 17071, DIN EN 14288-B, ISO 6452-B, SAE J 1756
- Volkswagen/AUDI: PV 3015
- GM/Opel: GME 60326-A; GMW 3235-B
- Toyota: TSM05036-B
- PSA Peugeot: D45 1727
- Beschlagprüfung (reflektometrisch )
- Normen: DIN 75201-A, DIN EN 14288-A, ISO 6452-A
- Volkswagen/AUDI: PV 3015; PV 3920
- Toyota: TSM05036-B
- PSA Peugeot: D45 1727
TYPISCHE MATERIALIEN, DIE GETESTET WERDEN
Beim Fogging-Test in der Kfz-Prüfung werden verschiedene Materialien untersucht, die im Fahrzeuginnenraum verwendet werden. Die wichtigsten Materialien, die diesem Test unterzogen werden, sind
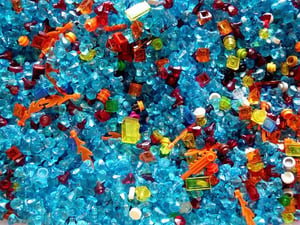
Verschiedene Arten von Kunststoffen für Armaturenbretter, Konsolen und andere Innenraumkomponenten
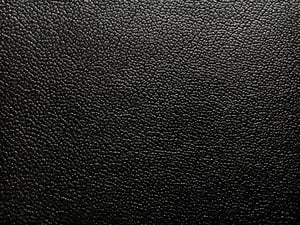
Speziell für Sitzbezüge und Lenkradbezüge
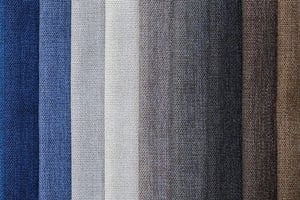
Stoffe, die für Sitzbezüge, Dachhimmel und andere Innenverkleidungen verwendet werden
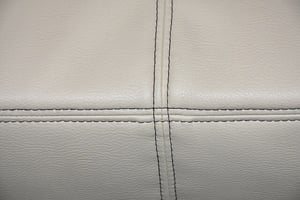
Als Alternative zu echtem Leder für verschiedene Innenraumkomponenten
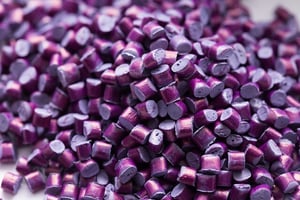
Gummiähnliche Materialien, die in verschiedenen Fahrzeugteilen verwendet werden
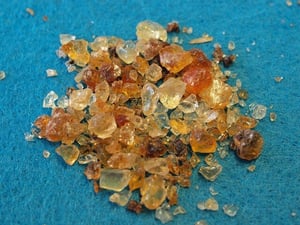
Dient der Verbindung verschiedener Komponenten im Fahrzeuginnenraum
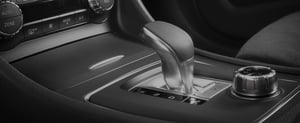
Verschiedene Oberflächeninspektionen für Innenteile
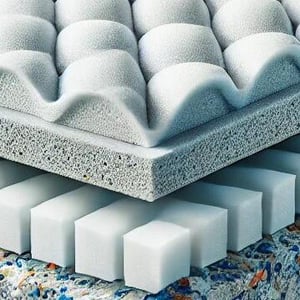
Speziell für Polstermöbel und Isolierung
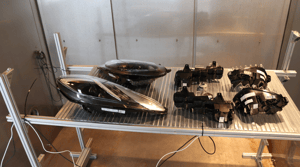
Kombinationen von verschiedenen Materialien im Fahrzeuginnenraum
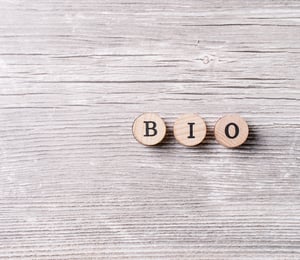
Neuere, umweltfreundliche Alternativen zu herkömmlichen Kunststoffen
WEITERE PRÜFUNGEN UND SERVICE
Vertrauen Sie auf über 30 Jahre Automotive-Testing Kompetenz
Häufig gestellte Fragen zum Nebeltest
Die für einen Fogging-Test erforderlichen Probenmengen hängen von der Norm und der verwendeten Prüfmethode ab. Hier sind die allgemeinen Richtlinien:
1. Norm DIN 75201 (Typ A und Typ B)
-
Typ A (Glasplattenmethode):
In der Regel ist eine Probenmenge von 10 cm² erforderlich. Die Probe wird auf eine beheizte Platte in einer abgedichteten Kammer gelegt, und die freigesetzten flüchtigen Stoffe kondensieren auf einer darüber liegenden Glasplatte. -
Typ B (Aluminiumfolienmethode):
Ähnlich wie bei Typ A wird ein Probenvolumen von etwa 10 cm² verwendet. Allerdings kondensieren die flüchtigen Substanzen auf einer gekühlten Aluminiumfolie.
2. Norm ISO 6452 (internationale Norm)
- Probenmenge:
Auch hier ist in der Regel eine Probengröße von etwa 10 cm² erforderlich, um die Menge der bei erhöhter Temperatur freigesetzten flüchtigen Stoffe zu ermitteln.
3. Andere spezifische Anforderungen
Je nach den spezifischen Anforderungen des Kunden oder der OEM-Normen können die Probenmengen variieren. Es ist wichtig, die jeweiligen Normen oder Prüfanforderungen sorgfältig zu prüfen.
Methode A - Reflektometrische Methode:
- Prinzip: Bei dieser Methode wird die Änderung des Reflexionsvermögens auf einer Glasplatte gemessen, auf der sich flüchtige Bestandteile aus der Materialprobe ablagern.
- Verfahren: Eine Materialprobe wird in einem Becherglas erhitzt, während eine darüber befindliche Glasplatte auf 21°C abgekühlt wird. Durch den Temperaturunterschied kondensieren die flüchtigen Bestandteile auf der Glasplatte. Der Reflexionsindex der beschlagenen Glasplatte wird dann gemessen, um die Menge des kondensierten Materials zu bestimmen.
- Anwendung: Diese Methode eignet sich besonders für Materialien, bei denen eine genaue Bestimmung des optischen Schleiereffekts erforderlich ist.
Methode B - Gravimetrische Methode:
- Prinzip: Bei dieser Methode wird das Gewicht der kondensierten flüchtigen Stoffe auf einer Aluminiumfolie gemessen.
- Verfahren: Die Materialprobe wird in einem Becherglas erhitzt, während eine Aluminiumfolienscheibe auf 21°C abgekühlt wird. Nach 16 Stunden wird die Menge des kondensierten Materials auf der Folie gewogen.
- Anwendung: Diese Methode ist ideal für eine genaue quantitative Bestimmung der Menge an kondensierten flüchtigen Stoffen.
JETZT KONTAKT AUFNEHMEN
EMISSIONEN UND GERUCH
Formaldehyd in Fahrzeugen: Herausforderungen für die Automobilindustrie
Mehr lesenStellantis: Freigabe für Emissionsprüfungen erfolgreich (VIAQ)
Mehr lesenVDA 277 vs. VDA 278: Was ist der Unterschied?
Mehr lesenGeruchsunterschiede bei Polypropylen: Die Rolle von Faserverstärkung und Verarbeitungsparametern
Mehr lesenWarum sind die Einheiten der Ergebnisse von Prüfungen der Werkstoffemissionen eigentlich so unterschiedlich?
Mehr lesenGrenzwerte für Formaldehyd und Formaldehydabspaltern in Fahrzeugen
Mehr lesenHÄUFIG GESTELLTE FRAGEN ZUM NEBELTEST
Um ein Beschlagen zu vermeiden, sollten Materialien , die für denEinsatz im Fahrzeuginnenraum vorgesehen sind, speziell getestet werden. Die Ergebnisse dieser Tests geben Aufschluss über die Eignung der Materialien und ermöglichen eine sinnvolle Auswahl zu treffen.