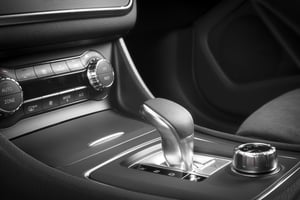
Fogging
Determination of the fogging behavior of materials used in vehicle interiors
FOGGING TEST IN THE
AUTOMOBILE INTERIOR
AGEING OF VEHICLE COMPONENTS IN SOLAR SIMULATION SYSTEMS
Exposure to the sun's rays is one of the most intense environmental influences to which automotive components are exposed. To ensure that materials and components can withstand the challenges of daily use, precise simulation of natural solar radiation under controlled conditions is essential. Our solar simulation tests offer a comprehensive solution for evaluating the long-term resistance of materials to radiation, heat and humidity.
Sun simulation is suitable for a wide range of applications: From vehicle exterior trim and paintwork to interior components and highly sensitive components such as charging cables for electric vehicles. Our tests simulate both outdoor and indoor conditions in order to reproduce real-life loads as accurately as possible.
With our expertise, we support automotive manufacturers and suppliers in meeting the industry's high quality standards and ensuring the durability of their products even under extreme conditions. Discover how our solar simulation helps to make the future of the automotive industry safer and more sustainable.
Fogging test methods
- DIN 75201-A (reflectrometric)
- DIN 75201-B (gravimetric)
- PV 3015 (Volkswagen)
- GMW 3235-A (General Motors Worldwide)
- PSA D45 1727
- and much more.
Test methods / specifications
- DIN 75220
- DBL 5471 (Mercedes-Benz)
- MBN 55555-5 § 5.1
- VDA 230-219
- VinFast VFDST00053800
- and much more.
Are you looking for an exam? Standard? Specifications?
Accredited & certified tests
CONTACT OUR EXPERTS
Description. Lorem ipsum dolor sit amet, consetetur sadipscing elitr, sed diam nonumy eirmod tempor invidunt ut labore et
- Tab Title
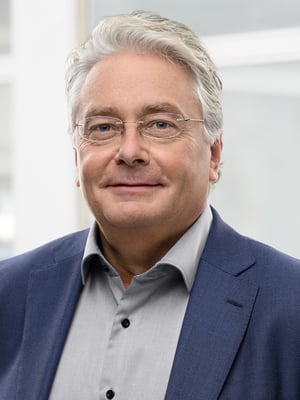
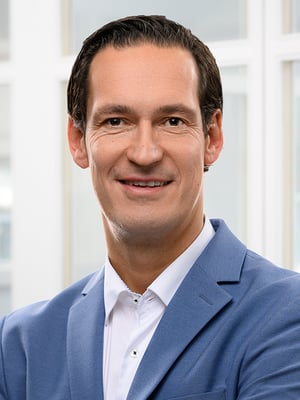
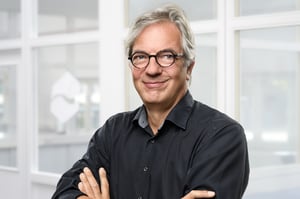
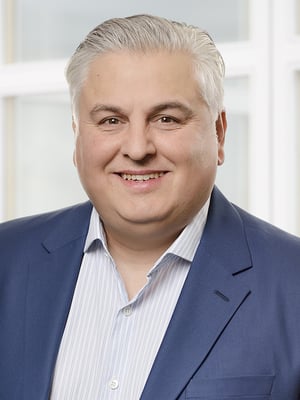
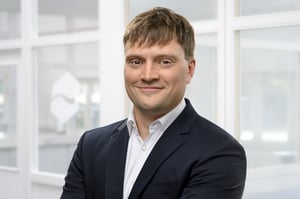
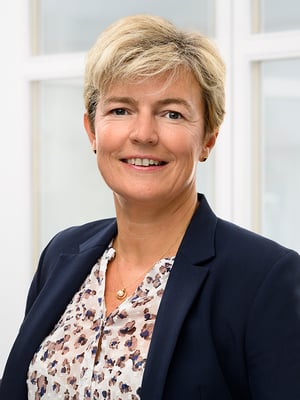
- Typical procedure
- Typical tests before and after ageing
- Test facilities
- Application examples
Typical SoSi test procedure
- Initial inspection: Before irradiation, the component is visually inspected to record important parameters such as color, gloss and material properties.
- Ageing in the solar simulation chamber: The component is exposed to a controlled environment with a defined irradiance and temperature/humidity profile.
- Temperature and humidity cycles: In addition to irradiation, temperature cycles (-40°C to +80°C) and controlled humidity values (up to 100% relative humidity) are frequently used.
- Intermediate tests: During the test cycle, checks are carried out to document changes such as fading, embrittlement or cracking.
- Final inspection: Once the test has been completed, a detailed final inspection is carried out to record changes of all kinds (e.g. color changes and structural damage).
- Report preparation: We provide a test report with detailed results, such as photo documentation and measurement data from the test.
- Return shipment (at the customer's request) of tested samples for further assessment
Typical tests before and after ageing
Before
- Visual evaluation
- Color and gloss measurement: metrological determination of color and gloss level
- Photogrammetry
- Scratch test
- Abrasion resistance/ abrasion resistance
- Emission and odor testing in the vehicle interior
Afterwards
- Visual evaluation
- Color & gloss: metrological change of color and evaluation according to the gray scale
- Photogrammetry
- Peel test (decorative goods )
- Foam adhesion
- Hardness test
Test facilities
- Test room volume: Our test rooms vary in size from 0.9 m³ to 46 m³ and therefore offer sufficient space for everything from small components to complete vehicles. This flexibility enables us to test a wide variety of materials andcomponentsunderlaboratoryconditions.
- Temperature range: Our test equipment is able to simulate temperatures from -60°C to +180°C. This enables comprehensive tests on temperature resistance and the ageing behavior of materials in hot and cold conditions.
- Humidity range: With a relative humidity of 10% to 98% , our test systems cover a wide range of climatic conditions. From dry desert conditions to the high humidity found in tropical climates, we are able to test the moisture resistance of materials and components.
Examples of components
Exterior components
- Paints and coatings
- Plastic body parts (e.g. bumpers )
- Headlights and rear lights
- Exterior mirrors and mirror seals
- aerials
- Windshield wipers
Interior components
- Instrument panel
- Parcel shelf
- Door panels
- Trim and molded upholstery parts for vehicle interiors (composite components )
- Dashboards
- Trim in the load compartment and trunk
- Interior trim
- Steering wheels
- Controls and switches
Special components
- Polymer automotive components
- Seals and rubber parts
- Plastics
- Adhesives and fasteners
- Charging sockets and charging cables for electric vehicles
- Sensors and cameras for driver assistance systems
- Components for car-to-car communication
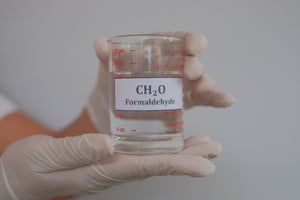
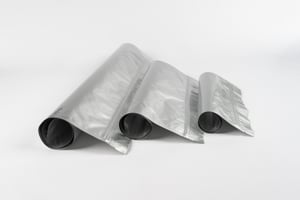
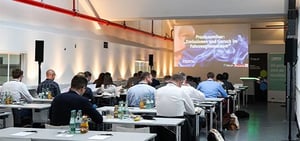
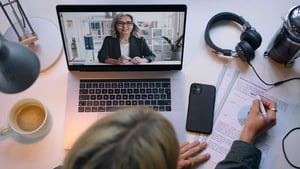
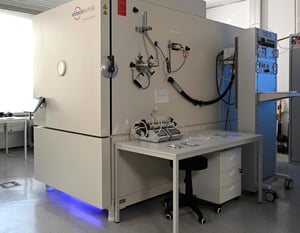
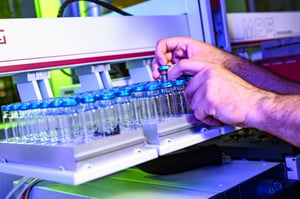
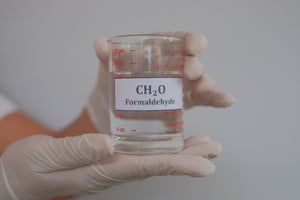
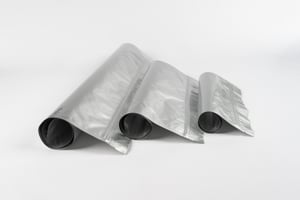
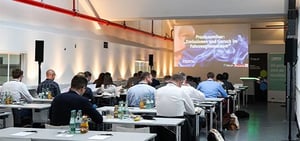
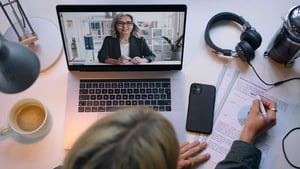
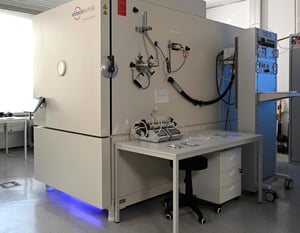
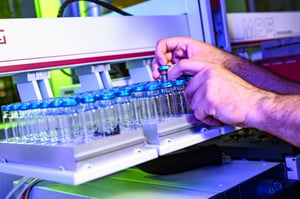
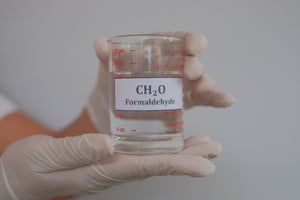
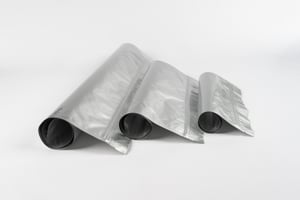
Frequently asked questions about the fogging test
The sample quantities required for a fogging test depend on the standard and the test method used. Here are the general guidelines:
1. standard DIN 75201 (type A and type B)
-
Type A (glass plate method):
A sample quantity of 10 cm² is typically required. The sample is placed on a heated plate in a sealed chamber and the volatiles released condense on a glass plate above. -
Type B (aluminum foil method):
Similar to type A, a sample volume of approximately 10 cm² is used. However, the volatile substances condense on a cooled aluminum foil.
2. standard ISO 6452 (international standard)
- Sample quantity:
Again, a sample size of about 10 cm² is typically required to evaluate the amount of volatiles released at elevated temperature.
3. other specific requirements
Depending on the specific requirements of the customer or OEM standards, sample quantities may vary. It is important to check the respective standards or test requirements carefully.
Method A - Reflectometric method:
- Principle: This method measures the change in reflectivity on a glass plate on which volatile components from the material sample are deposited.
- Procedure: A material sample is heated in a beaker while a glass plate above it is cooled to 21°C. The temperature difference causes the volatile components to condense on the glass plate. The reflectance index of the fogged glass plate is then measured to determine the amount of condensed material.
- Application: This method is particularly suitable for materials for which an exact determination of the optical fog effect is required.
Method B - Gravimetric method:
- Principle: This method measures the weight of condensed volatiles on an aluminum foil.
- Procedure: The material sample is heated in a beaker while an aluminum foil disc is cooled to 21°C. After 16 hours, the amount of condensed material on the foil is weighed.
- Application: This method is ideal for an accurate quantitative determination of the amount of condensed volatiles.
CONTACT US
ENVIRONMENTAL SIMULATION
Korrosion
Read moreWas versteht man unter Umweltsimulation im automobilen Kontext?
Read moreSteinschlagprüfungen - Sicherheit auf der Straße beginnt im Labor
Read moreKorrosion
Read moreWas versteht man unter Umweltsimulation im automobilen Kontext?
Read moreSteinschlagprüfungen - Sicherheit auf der Straße beginnt im Labor
Read moreKorrosion
Read moreWas versteht man unter Umweltsimulation im automobilen Kontext?
Read moreSteinschlagprüfungen - Sicherheit auf der Straße beginnt im Labor
Read moreFREQUENTLY ASKED QUESTIONS ABOUT CLIMATE AUDITS
Yes, we carry out tests in accordance with national and international standards as well as OEM-specific requirements and are accredited for the most important tests. Find out more about our accreditations here.